航空航天制造MES系统,智能化升级如何破解生产管理难题?
在精密程度要求极高、工艺复杂度堪称“制造业明珠”的航空航天领域,生产管理的每一个环节都容不得丝毫误差。从零部件的超精密加工到整机装配的全流程协同,传统依赖人工和经验驱动的管理模式已难以满足现代航空航天制造对效率、质量与可追溯性的严苛要求。如何通过数字化工具实现生产透明化、过程可控化,成为行业升级的关键突破口。而制造执行系统(MES)的深度应用,正在为这一难题提供系统性解决方案。
一、航空航天制造业的四大核心痛点
- 多层级生产协同效率低下 航空航天产品涉及上千家供应商与多级生产单元,传统信息传递依赖纸质单据或分散系统,易导致计划延迟、资源冲突。
- 质量追溯成本高昂 行业对零部件全生命周期追溯要求严苛,但人工记录易出错,返工或召回时难以快速定位问题源头。
- 工艺参数动态管理不足 特殊材料加工(如钛合金、复合材料)需实时监控温度、压力等参数,传统方式难以及时干预异常工况。
- 合规性压力持续升级 AS9100、适航认证等标准对文档管理、过程验证提出更高要求,人工核验难以保障零缺陷目标。
二、MES系统的功能架构与行业适配性
航空航天MES系统并非通用型解决方案,而是针对行业特性进行深度定制的“中枢神经”,其核心模块包括:
- 智能计划排程:基于订单优先级、设备负载及物料齐套性,动态生成最优生产路径。
- 实时工艺监控:通过物联网(IoT)采集设备数据,自动比对工艺规范,触发预警机制。
- 质量闭环管理:集成SPC(统计过程控制)工具,实现从原材料入库到成品交付的全流程质量档案。
- 追溯与合规支持:以唯一标识码(如二维码)串联工序数据,一键生成符合适航要求的审计报告。
三、MES系统的差异化竞争优势
- 打破数据孤岛,实现端到端透明化 通过打通ERP、PLM与车间设备,MES构建了从设计到交付的数据闭环,管理层可实时查看生产进度、瓶颈工序与资源利用率。
- 预防性质量管控 借助AI算法分析历史数据,系统能预测潜在工艺偏差,在加工超差前主动调整参数,降低废品率。
- 柔性响应变更需求 面对客户规格调整或供应链波动,MES可快速重组生产计划,平衡交期与成本,提升订单履约能力。
- 降低合规风险 自动化记录生产数据并加密存储,确保符合AS9100D等标准对过程可审计性的要求。
四、MES在航空航天制造中的典型应用场景
- 高价值零部件制造:针对发动机叶片等关键部件,MES精准管控每一道热处理、涂层工艺的参数合规性。
- 总装线协同调度:通过电子看板与移动终端,实现装配工位间的物料精准配送与异常快速响应。
- 供应链双向追溯:从原材料批次到供应商生产批次,系统支持跨企业层级的正向/反向追溯,缩短质量问题排查周期。
总结
航空航天制造的数字化转型,本质是通过数据驱动重构生产管理逻辑。MES系统以其对车间层业务的深度覆盖能力,正在成为企业实现“精益化、智能化、合规化”的核心引擎。未来,随着数字孪生、边缘计算等技术的融合,MES将进一步推动航空航天制造从“经验决策”向“模型驱动”跨越。
问答部分
Q1:MES系统如何帮助航空航天企业应对多品种、小批量生产挑战? A1:航空航天产品具有高度定制化特征,传统计划排程难以适应频繁的订单变更。MES系统通过以下方式破解这一难题:首先,基于规则引擎与仿真技术,快速评估新订单对现有产能、物料库存的影响,生成可行排产方案;其次,通过模块化工序配置,支持工艺路线的灵活重组,减少换型时间;最后,利用实时数据反馈动态调整生产节奏,确保关键资源(如高精度机床)的利用率最大化。这种敏捷响应能力,显著降低了小批量生产导致的边际成本上升。 Q2:航空航天MES系统在质量管控方面有哪些独特设计? A2:针对行业对“零缺陷”的极致追求,MES的质量管理模块强化了三层控制机制:其一,在工序级嵌入防错验证,例如通过视觉检测自动判断装配完整性,拦截未达标半成品流入下道工序;其二,整合SPC工具,对关键参数(如焊接温度)进行趋势分析,触发预警而非事后补救;其三,建立跨系统的质量数据湖,将设计规范、工艺标准、检验记录关联分析,定位系统性风险点。这种“预防-监控-改进”闭环,大幅降低了质量成本。 Q3:MES系统与ERP在航空航天制造中的协同关系是什么? A3:ERP与MES分别聚焦于企业资源计划与车间执行层,二者的协同是数字化落地的关键。ERP向MES传递主生产计划、物料需求及成本目标,而MES将实时生产数据(如工单进度、设备状态)反馈至ERP,支持财务核算与供应链优化。在航空航天场景中,这种协同进一步深化:MES基于ERP的交付周期要求,反向优化工艺路线;ERP则利用MES采集的工时、能耗数据,完善产品全成本模型。这种双向集成消除了管理层与执行层的信息断层,助力企业实现战略与运营的统一。
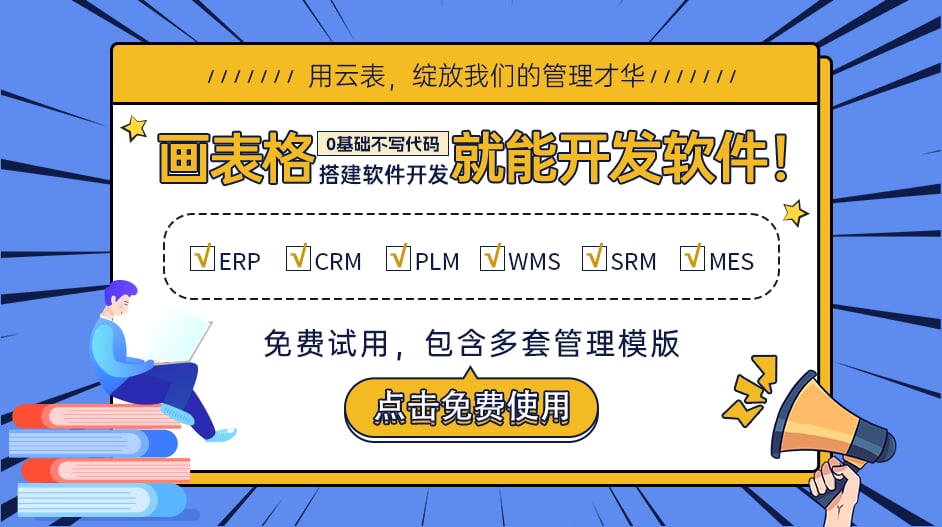