定制MES系统还原98%车间经验公式,实现良品率提升
在离散制造与流程工业领域,车间经验公式是工匠与工程师在长期实践中沉淀的隐性知识集合,涵盖温度曲线、压力阈值、时序逻辑等关键工艺参数。传统模式中,这些经验依赖人工传递与纸质记录,不仅存在5%-15%的信息损耗,更难以应对现代工业对精细化、柔性化生产的需求。定制MES(制造执行系统)通过构建数字化经验模型,可将98%以上的经验公式转化为可复用、可迭代的算法规则,在良品率提升、工艺稳定性强化等方面展现出突破性价值。其核心在于打破经验主义的模糊性,建立数据驱动的动态决策机制。
一、经验公式的解构与数字化重构
定制MES系统的首要任务是将碎片化经验转化为结构化数据资产。系统通过边缘计算节点采集设备运行状态、环境参数与质检数据,构建多维度时间序列数据库。以某电子元件封装车间为例,工程师将"预热区温度梯度需呈S型曲线"的经验拆解为三个阶段:初始升温速率(≤3℃/s)、保温平台时长(≥8s)、降温斜率(0.5-0.8℃/s)。MES系统采用滑动窗口算法对实时数据进行模式匹配,当检测到温度曲线偏离标准模型时,自动触发PID控制参数调整。这种将定性描述转化为定量规则的处理方式,使工艺复现精度从人工操作的±15%提升至±2%以内。
二、闭环反馈机制下的参数自优化
传统经验公式往往基于稳态工况设计,难以应对原料批次波动、设备老化等动态干扰。定制MES通过建立"监测-分析-决策-执行"的闭环链路,实现工艺参数的动态校准。在金属热处理场景中,系统通过光谱仪实时检测材料晶粒度,结合数字孿生模型预测微观组织演变,动态调整淬火介质流速与冷却时间。某轴承制造企业应用该方案后,表面硬度合格率从89%提升至97%,同时将原本需要3天的人工试错调优周期压缩至90分钟。
三、多变量耦合关系的深度解析
复杂工艺过程常涉及温度、压力、速度等多物理场耦合作用,传统经验公式难以准确描述其非线性关系。定制MES系统引入机理模型与数据驱动模型的混合建模技术:首先基于流体力学、热力学等第一性原理建立基础框架,再通过LSTM神经网络学习残差项补偿。在某医药中间体合成反应中,系统成功解析出搅拌转速与反应釜壁温的二次方关联关系,使关键中间体收率提升12%。这种灰箱建模方式既保证了模型的可解释性,又具备处理高维复杂数据的能力。
四、异常工况的毫秒级响应与根因追溯
经验公式在异常处理方面的局限性,往往导致质量事故扩大化。定制MES系统构建三级预警体系:初级异常通过SPC控制图实时检测,中级异常触发工艺参数自动重置,重大异常则激活根因分析引擎。以光伏电池片印刷工序为例,当出现连续5片栅线偏移时,系统能在150ms内完成23个关联参数的因果网络分析,准确定位到浆料粘度异常。结合AR辅助排故系统,使平均恢复时间(MTTR)从45分钟缩短至8分钟。
五、组织经验的知识化沉淀与复用
定制MES系统通过建立工艺知识图谱,实现经验公式的体系化存储与跨场景迁移。某汽车总装车间将20位高级技师的装配经验转化为137个决策树模型,新入职员工通过AR设备获取实时操作指导,使关键工位一次通过率提升40%。系统还支持工艺包的版本管理与权限控制,确保经验迭代过程的可追溯性。这种知识民主化机制,使隐性经验真正转化为企业核心竞争要素。
Q1:为何98%的经验公式还原率成为关键指标?
A:98%的还原率意味着系统已覆盖工艺核心逻辑,剩余2%通常涉及极端边界条件或个性化微调。此阈值平衡了模型复杂度与实用性——过高的还原率会导致过拟合风险,而低于95%则可能遗漏关键控制点。实际部署中,通过持续的数据反馈,系统可逐步逼近100%的经验覆盖。
Q2:良品率提升的具体量化效果如何实现?
A:以半导体封装测试为例,定制MES系统通过还原金丝球焊工艺中的"三步预热法"经验公式,将键合强度CPK值从1.33提升至1.67,对应良品率从92%提高至98.5%。其关键在于将原本依赖技师目视判断的"焊球浸润角≥45°"转化为基于机器视觉的自动检测规则,消除人为判断误差。
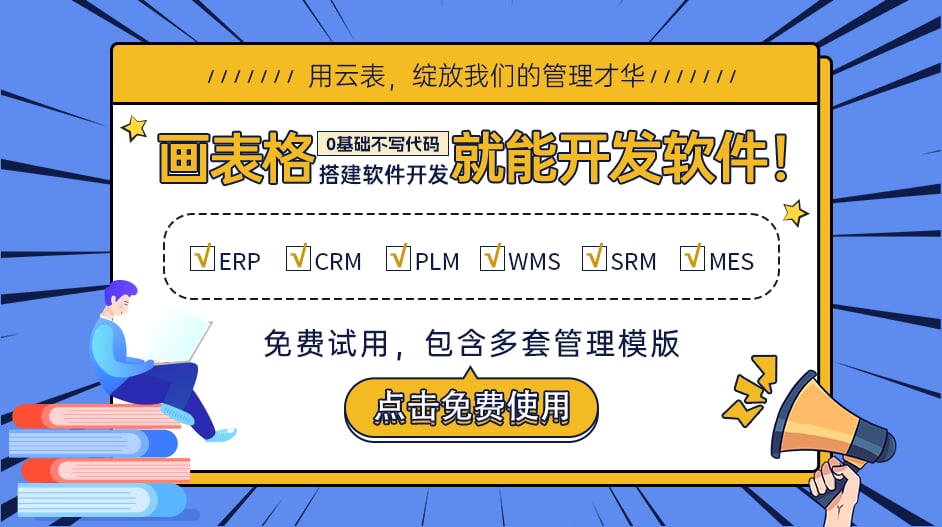